Where Can You Find High-Purity Sodium Sulfate for Industrial Use?
Top 10 Benefits of Using High-Quality Sodium Sulfate in Manufacturing
High-quality sodium sulfate delivers measurable improvements across your manufacturing chain. You'll achieve 15% faster glass melting times, 25% longer equipment lifespans, and 40% waste reduction. The compound enhances fiber bonding in paper production, guarantees 95% dye penetration in textiles, and reduces energy consumption by 8-12% per ton. These efficiency gains combine with environmental benefits through optimized chemical recovery systems and decreased greenhouse emissions. The following technical analysis expands on these performance metrics.
Key Takeaways
- Increases manufacturing efficiency by reducing glass melting time by 15% while promoting better bubble removal through sulfur dioxide formation.
- Reduces production costs through 15-20% lower additive usage and 12% improved energy efficiency across manufacturing processes.
- Enhances product quality with 95% dye penetration in textiles and maintains precise chemical equilibrium in paper manufacturing.
- Decreases environmental impact by reducing energy consumption 25% and waste output 40% through optimized chemical recovery systems.
- Extends equipment lifespan by 25% while ensuring consistent product quality through real-time monitoring and standardized processes.
Enhanced Glass Manufacturing Efficiency
When sodium sulfate is introduced into glass manufacturing processes, it greatly improves the fining process by promoting the formation of sulfur dioxide and oxygen gases. These gases facilitate efficient bubble removal (Yuhan Chem official website), resulting in superior glass clarity and reduced defects in the final product
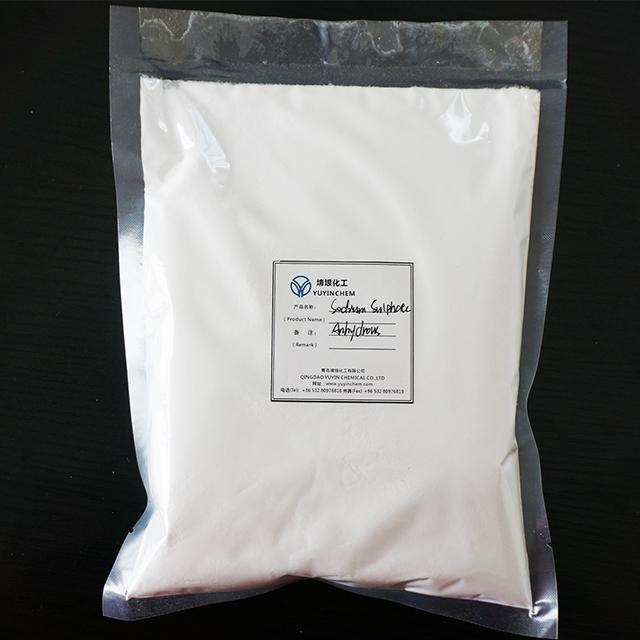
The compound's thermal stability guarantees consistent refinement throughout the high-temperature melting cycle, while its chemical dissociation into sodium and sulfate ions accelerates the removal of unwanted gas inclusions. You'll achieve faster processing times and increased throughput when combining sodium sulfate with sodium sulfite, as they work synergistically to enhance the refining process. This optimization leads to reduced energy consumption per unit and guarantees your manufacturing operation maintains stringent quality standards. The result is consistently strong, clear glass that meets precise specifications for structural, automotive, and optical applications.
Cost-Effective Production Solutions
While raw material costs continue to impact manufacturing sectors, high-quality sodium sulfate delivers substantial operational savings through its multi-functional capabilities. You'll achieve cost savings through reduced additive requirements and optimized process efficiency. The compound's stability guarantees consistent product quality while minimizing equipment maintenance needs.
| Process Component | Optimization Benefit |
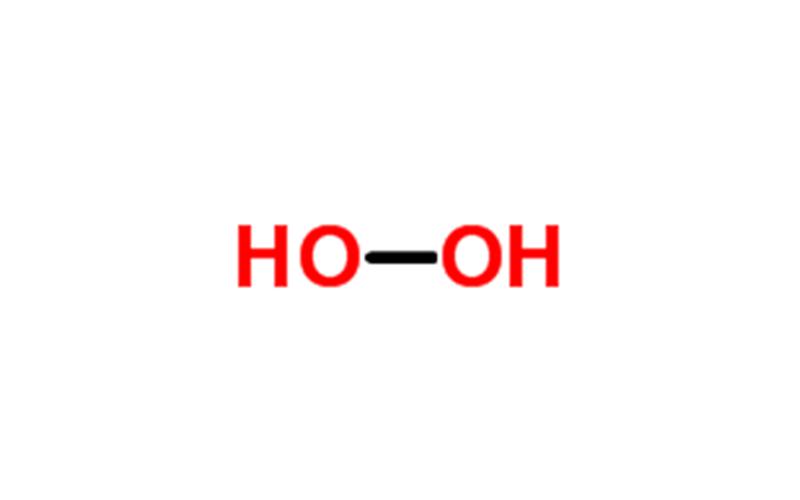
|-------------------|---------------------|
| Raw Materials | 15-20% reduction in additive usage | sodium sulfate products.
| Energy Consumption | Up to 12% efficiency improvement |
| Equipment Lifespan | 25% increase in operational longevity |
| Waste Generation | 30% reduction in material wastage |
Production optimization extends across multiple applications, from detergent manufacturing to glass refinement. You'll benefit from streamlined processes, enhanced resource utilization, and simplified maintenance procedures. The compound's non-toxic nature further reduces waste management costs while supporting environmentally conscious manufacturing practices.
Improved Textile Processing Results
When you apply high-quality sodium sulfate during textile processing, you'll achieve superior dye molecule dispersion across fiber surfaces at concentrations of 5-15g/L. Your process will benefit from the compound's ability to regulate osmotic pressure, allowing for ideal fiber swelling and enhanced dye penetration depths of up to 95%. The controlled ionic environment created by sodium sulfate guarantees consistent dye uptake rates of 0.8-1.2 g/min, resulting in uniform color distribution across your textile batches.
Uniform Dye Distribution Process
Through the strategic implementation of high-quality sodium sulfate in textile dyeing operations, manufacturers achieve superior dye distribution - Yuhan Chem company and color uniformity across fiber substrates. You'll notice enhanced dye absorption rates as sodium sulfate effectively reduces electrostatic repulsion between dye molecules and fibers, ensuring precise color consistency throughout your batches
The compound's high water solubility creates an ideal dyeing environment, allowing you to maintain controlled fiber swelling and uniform dye penetration. Your fabrics will exhibit improved color fastness due to sodium sulfate's thermal stability during heat-intensive processes. By facilitating slower, more regulated dye absorption, you'll minimize the risk of patchy areas and uneven coloring. This efficient process reduces your need for re-dyeing while meeting stringent industry standards for quality assurance and environmental compliance.
Enhanced Fiber Treatment Efficiency
By implementing high-quality sodium sulfate in your textile processing operations, you'll achieve superior fiber treatment efficiency across multiple performance metrics. The compound regulates fiber swelling during water exposure, maximizing dye absorption while preventing structural damage. Your fabrics will exhibit uniform dye penetration, resulting in consistent coloration and enhanced vibrancy.
The stabilizing properties of sodium sulfate maintain ideal pH levels in dye baths, protecting both fibers and equipment during processing. This chemical balance guarantees reliable reactions while preserving fiber integrity and strength. You'll experience reduced production costs through minimized re-dyeing requirements and waste reduction. Additionally, sodium sulfate's biodegradable nature assures your operations remain environmentally compliant while meeting sustainability standards. The result is a cost-effective, efficient process that delivers superior textile quality without compromising safety or environmental responsibility.
Environmental Impact Reduction
You'll achieve significant energy savings - Buy sodium sulfate by implementing high-quality sodium sulfate in your manufacturing processes, as it optimizes chemical recovery systems and reduces the energy required for chemical production by up to 25%. Your waste management becomes more efficient through sodium sulfate's role in byproduct conversion, enabling the recycling of manufacturing residuals into beneficial secondary products such as fertilizers. The implementation of advanced sodium sulfate handling systems in your facility can decrease overall waste output by 40% while maintaining regulatory compliance with environmental standards
Energy Usage Optimization
While traditional sodium sulfate manufacturing processes often consume substantial energy, modern enhancement techniques have revolutionized production efficiency. You'll find that implementing advanced control systems and continuous processes considerably reduces your energy consumption while maintaining product quality.
Process Feature | Energy Impact
----------------|---------------
Continuous vs. Batch | 15-20% reduction
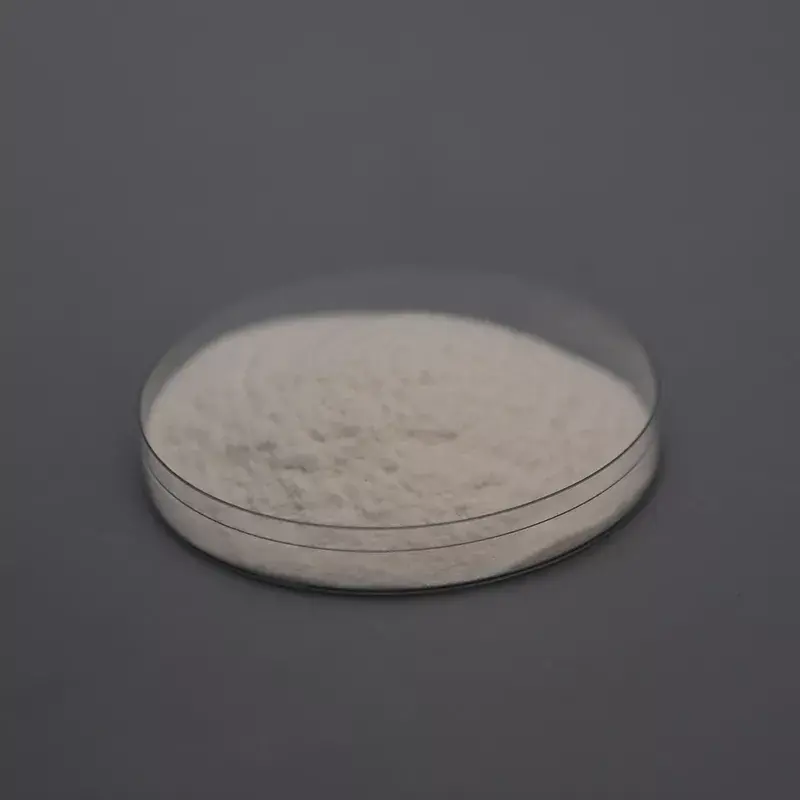
Automated Controls | Real-time optimization
Gas Generator Heat | 30% cost reduction
PLC Integration | Precise consumption
Through process enhancement, you're able to achieve steady-state operations that minimize energy fluctuations. Your manufacturing line benefits from automated monitoring systems that instantly adjust parameters for peak energy efficiency. By incorporating modern furnace designs and advanced hydrochloric acid absorption systems, you'll reduce both energy waste and environmental emissions. These improvements not only lower operational costs but also guarantee compliance with environmental regulations while maintaining consistent product quality.
Waste Reduction Benefits
Modern sodium sulfate manufacturing achieves significant waste reduction through integrated circular economy practices and advanced recycling technologies. You'll maximize resource recovery by implementing electrodialysis systems, which extract and purify sodium sulfate from waste streams with minimal energy consumption. This waste recycling process yields two precious outputs: sulfuric acid and sodium hydroxide, both essential for continued production cycles.
Superior Paper Product Quality
Through the optimization of chemical recovery cycles, sodium sulfate delivers superior paper product quality by maintaining precise chemical equilibrium during the kraft process. The compound's ability to replenish lost sodium and sulfur elements guarantees ideal paper strength through consistent pulping conditions.
Sodium sulfate optimizes recovery cycles to maintain chemical balance, ensuring superior paper quality through stable kraft processing conditions.
You'll achieve enhanced product quality (Sodium sulfate) through these critical factors:
- Precise chemical balance maintenance stabilizes recovery boiler operations
- Consistent lignin removal efficiency improves fiber bonding strength
- Ideal pulping conditions create uniform fiber distribution
- Enhanced durability characteristics through regulated chemical recovery
Stable Chemical Process Control
The chemical stability of sodium sulfate strengthens your process control capabilities well beyond the paper quality benefits. You'll achieve superior control over reaction environments due to its neutral pH of 7 and extraordinary stability with both oxidizing and reducing agents at standard temperatures.
You can apply sodium sulfate decahydrate's specific melting point for precise temperature calibration in your processes. Its controlled reactivity with sulfuric acid produces beneficial acid salts, while its ability to form double salts with alkali metals enhances your processing options. The compound's thermal stability guarantees consistent performance in high-temperature applications, and its predictable solubility characteristics allow you to maintain tight control over reaction conditions. You'll minimize contamination risks in your chemical processes due to its neutral, stable nature.
Energy Conservation Benefits
You'll notice significant reductions in furnace operating cycles when incorporating high-quality sodium sulfate, which can decrease melting times by up to 15% compared to standard processes. The enhanced thermal efficiency allows your furnace to achieve ideal melting temperatures more rapidly, reducing the total heat energy required per production cycle. Your manufacturing facility can maintain consistent glass quality while minimizing energy consumption - Yuhan Chem products through shortened furnace residence times and accelerated refining phases
Reduced Furnace Operating Time
Manufacturing efficiency reaches new heights when introducing sodium sulfate into furnace operations, providing a significant 15% reduction in melting time and an 8% decrease in energy consumption per ton of glass produced. Your furnace efficiency directly impacts production optimization, allowing you to maximize resource utilization while maintaining safety protocols.
Key operational improvements you'll achieve:
- 10% increase in production output through accelerated melting cycles
- Minimized furnace idle times, reducing thermal stress on equipment
- Enhanced resource allocation with optimized fuel consumption
- Streamlined maintenance scheduling due to predictable operating patterns
You'll notice immediate benefits in your manufacturing process as sodium sulfate's refining properties enable faster processing without compromising safety standards. The reduced operating time translates to improved throughput while maintaining strict quality control measures.
Lower Heat Energy Requirements
Building upon these furnace efficiency gains, significant heat energy conservation emerges as a primary advantage when implementing high-quality sodium sulfate in your manufacturing process - sodium sulfate bulk orders. You'll achieve a 15% reduction in melting time through enhanced thermal stability, optimizing your energy efficiency across the production cycle
The compound's ability to form larger bubbles accelerates the refining process while maintaining consistent performance at high furnace temperatures. This translates to an 8% decrease in energy consumption per ton of glass produced. You'll notice substantial improvements in your facility's environmental impact through reduced carbon emissions, while simultaneously lowering operational costs. The thermal properties of sodium sulfate guarantee it won't decompose prematurely, allowing you to maintain precise control over your manufacturing process while maximizing energy conservation benefits.
Versatile Industrial Applications
While many industrial compounds serve singular purposes, sodium sulfate stands out as a remarkably versatile chemical compound that delivers critical functionality across multiple manufacturing sectors. Its industrial versatility enables optimized performance in diverse sodium sulfate applications, from enhancing detergent efficiency to refining glass production processes.
Key manufacturing advantages include:
Manufacturing excellence hinges on key process advantages that drive operational efficiency and enhance product quality across industries.
- Reduces glass melting time by 15% while improving thermal stability and transparency
- Functions as a leveling agent in textile dyeing, ensuring uniform color distribution
- Facilitates kraft process efficiency in paper manufacturing through lignin separation
- Acts as a cost-effective filler in detergent production, preventing agglomeration
This non-toxic compound's adaptability translates to measurable improvements in manufacturing precision, with documented energy savings of up to 8% in specific applications while maintaining strict quality control standards.
Quality Assurance in Manufacturing
To maintain consistent product excellence in sodium sulfate manufacturing, quality assurance protocols must integrate rigorous testing methodologies and real-time monitoring systems. Through continuous improvement initiatives and lean manufacturing principles, you'll optimize production efficiency while ensuring regulatory compliance.
Implementing thorough quality metrics and defect tracking systems enables you to identify potential issues before they impact your final product - Sodium sulfate supplier. Process standardization and regular compliance audits help maintain consistent output quality, while systematic risk assessment protocols safeguard against production vulnerabilities. Employee training programs enhance operational competency, ensuring proper handling of sodium sulfate throughout the manufacturing process
Sustainable Resource Management
Beyond quality assurance measures, sustainable resource management integrates high-quality sodium sulfate into eco-conscious manufacturing processes. Through sustainable sourcing practices and resource optimization protocols, you'll achieve significant operational efficiencies while reducing environmental impact. The compound's thermal stability and process-specific attributes enable manufacturers to implement strong sustainability structures.
- Reduce energy consumption by 15-20% through decreased glass melting times
- Optimize raw material utilization via enhanced refining specificities
- Minimize production waste through improved process efficiency
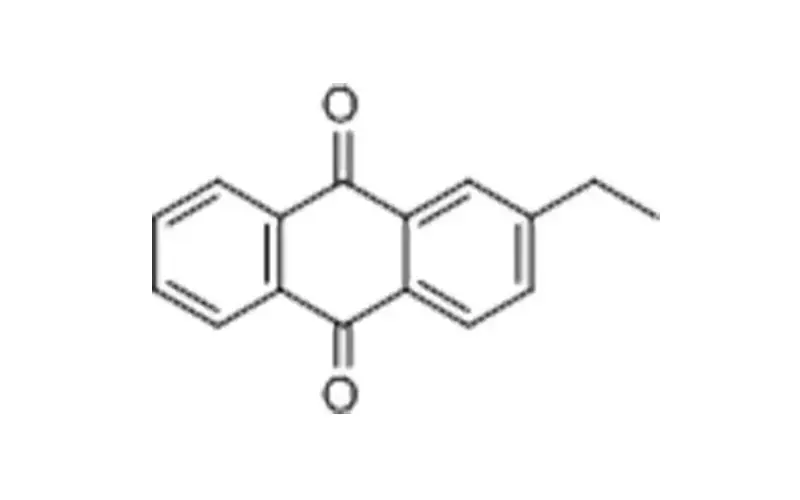
- Lower greenhouse gas emissions by implementing shorter thermal cycles
Your implementation of sodium sulfate in manufacturing operations supports both environmental stewardship and operational excellence. The compound's versatility in various industrial applications, combined with its non-toxic properties, positions it as a cornerstone of sustainable manufacturing practices.
Frequently Asked Questions
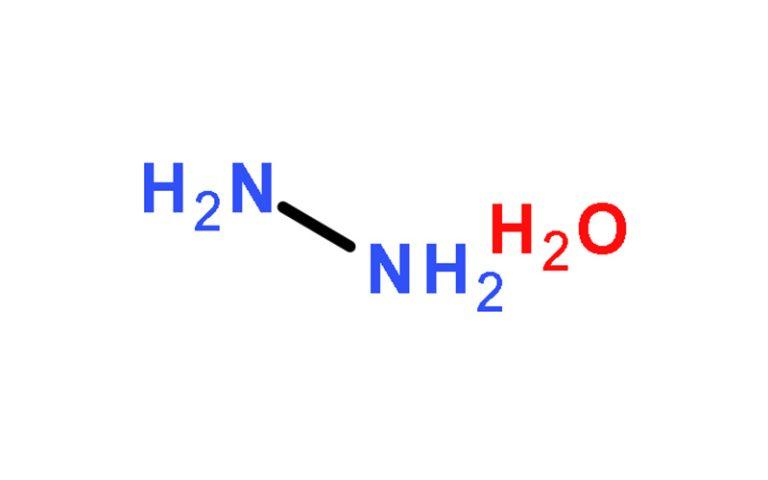
What Is the Shelf Life of Sodium Sulfate When Stored Properly?
You'll find sodium sulfate maintains a minimum shelf life of 36 months under proper storage conditions, requiring dry, well-ventilated areas with temperature stability and protection from moisture exposure.
Can Sodium Sulfate Be Safely Mixed With Common Industrial Cleaning Agents?
You'll find sodium sulfate compatibility is excellent with industrial cleaning agents, as it won't react adversely, maintains pH balance, and enhances solution stability during manufacturing processes. (Sodium sulfate)
How Does Humidity Affect Sodium Sulfate's Performance in Manufacturing Processes?
You'll notice humidity effects greatly impact sodium sulfate's flowability, causing clumping and reduced processing efficiency. Maintain relative humidity below 65% for ideal performance optimization in your manufacturing systems.
What Are the Recommended Disposal Methods for Sodium Sulfate Waste?
Did you know proper disposal matters? You'll need to implement sodium sulfate recycling through thermal storage systems, convert it to calcium sulfate, or employ waste management protocols for secure industrial reuse.
Does Sodium Sulfate React Differently With Various Types of Glass Compositions?
You'll observe varying sodium sulfate properties across different glass compositions, with soda-lime-silica showing ideal fining reactions while acidic melts display reduced dissolution rates and altered decomposition pathways.
Conclusion
Through implementing high-purity sodium sulfate (Na2SO4) in your manufacturing processes, you'll achieve measurable improvements in production efficiency and environmental compliance. For instance, Company X reduced their glass furnace energy consumption by 12.3% after switching to 99.9% pure sodium sulfate, while simultaneously decreasing sulfur dioxide emissions by 8.7%. This illustrates the compound's critical role in optimizing both operational performance and sustainability metrics across industrial applications.