Cut Fleet Maintenance Costs by 30% with These Software Solutions
10 Proven Ways to Boost Construction Fleet Performance With Advanced Tracking
Advanced tracking technologies offer ten proven ways to enhance your construction fleet's performance. You'll benefit from real-time vehicle monitoring, improved route planning, and predictive maintenance scheduling. Fuel consumption analysis and driver behavior assessment help cut costs and improve safety. Implement automated reporting systems, geofencing for site management, and strategies to reduce equipment downtime. Integrate fleet management with project management systems for seamless operations. Asset utilization tracking guarantees efficient resource allocation. By leveraging these data-driven solutions, you'll increase productivity, reduce expenses, and streamline your construction operations. Uncover how each strategy can revolutionize your fleet management approach.
Key Takeaways
- Real-time vehicle monitoring provides insights into fleet operations and enhances driver accountability.
- Optimized route planning integrates traffic data and multi-stop algorithms to improve efficiency and timeliness.
- Predictive maintenance scheduling prevents unexpected breakdowns and optimizes maintenance intervals.
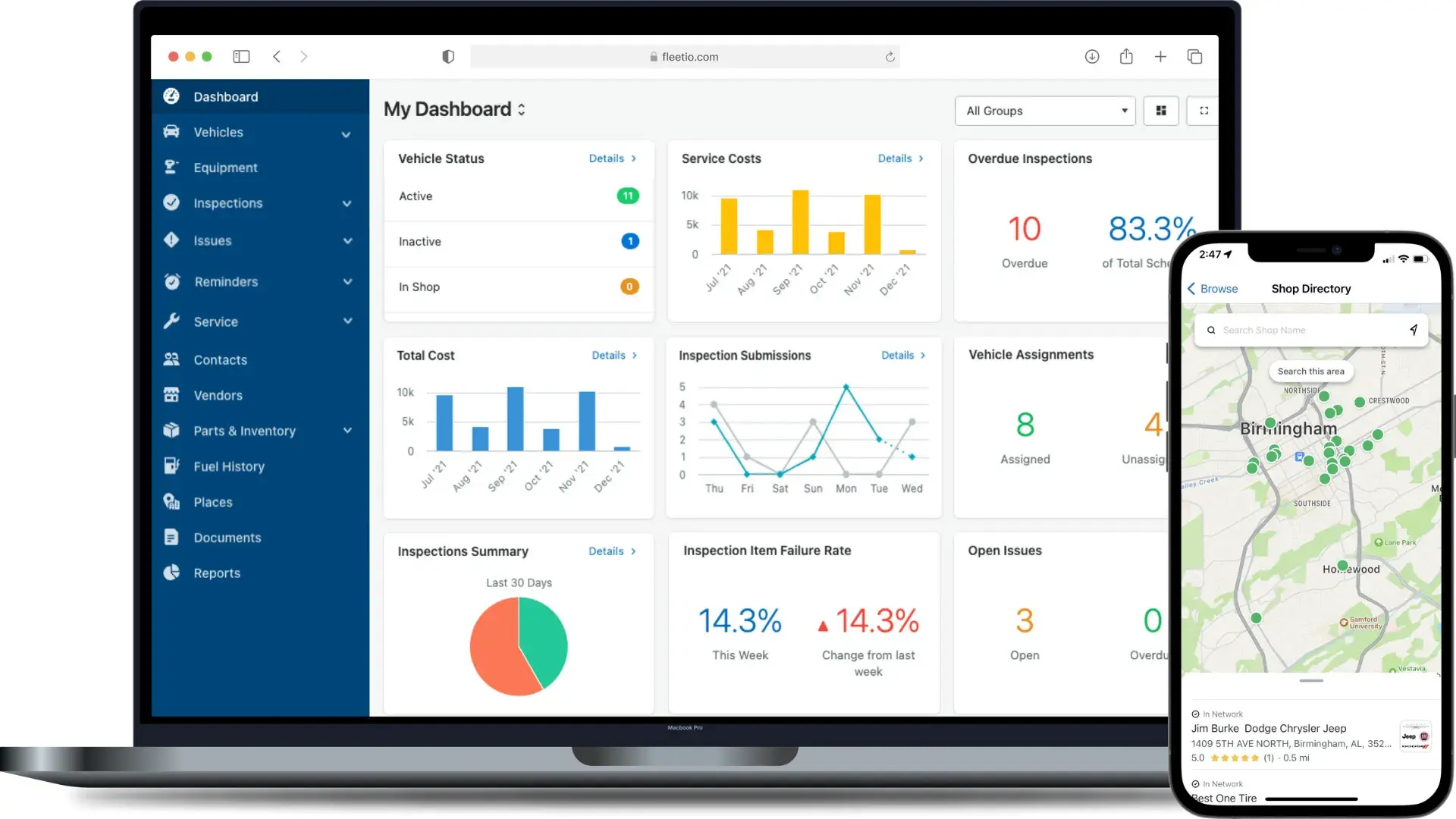
- Fuel consumption analysis identifies inefficiencies and leads to cost savings and reduced environmental impact.
- Driver behavior assessment evaluates habits and implements accountability measures to ensure responsible driving practices.
Real-Time Vehicle Monitoring
Real-time vehicle monitoring serves as the cornerstone of modern construction fleet management. By implementing advanced tracking technology, you'll gain unparalleled understanding into your fleet's operations. This system continuously monitors vehicle health, allowing you to predict maintenance needs and prevent costly breakdowns. You'll also enhance driver accountability through real-time location tracking and performance metrics.
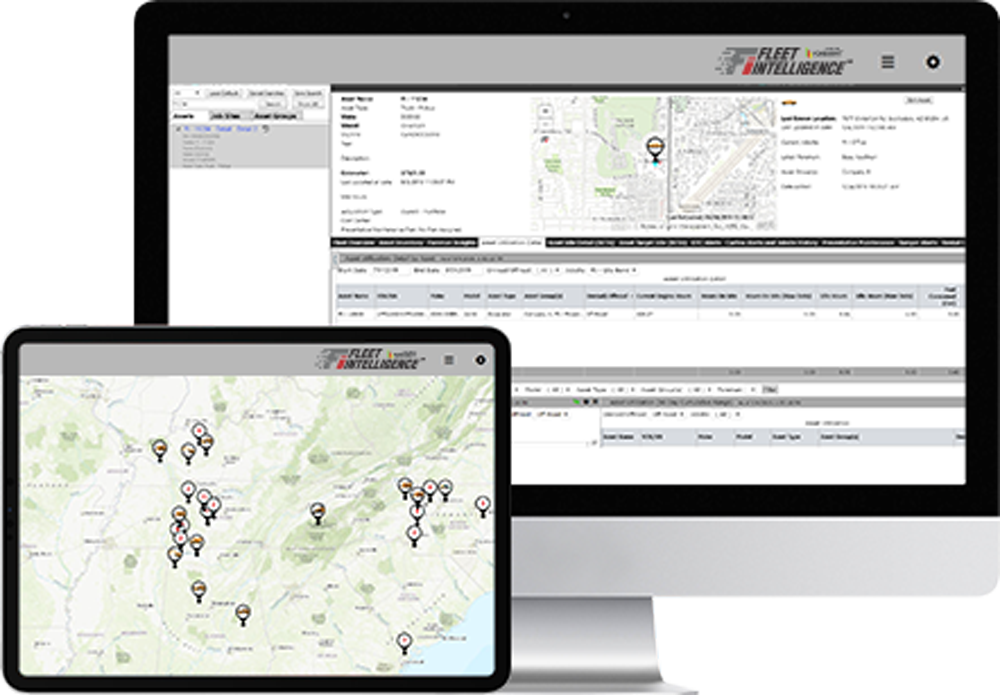
As your fleet grows, scalability becomes essential. Modern tracking solutions offer seamless integration for new vehicles, ensuring your monitoring capabilities expand with your fleet. Compliance monitoring features help you adhere to industry regulations and safety protocols, reducing the risk of fines and accidents.
Data analytics play an important role in extracting beneficial operational knowledge from the wealth of information collected. You'll identify maintenance trends, optimize routes, and improve overall efficiency. In the event of theft, asset recovery becomes much easier with real-time location data.
Optimized Route Planning
You'll enhance your construction fleet's efficiency through optimized route planning. By integrating real-time traffic data, you can flexibly adjust routes to avoid congestion and minimize delays. Implement multi-stop optimization algorithms to streamline deliveries and pickups, while utilizing geofencing technology to automate site-specific workflows and improve overall operational efficiency.
Real-Time Traffic Data Integration
Integrating real-time traffic data into route planning systems is a revolutionary advancement for construction fleet management. This technology allows you to flexibly adjust routes based on current road conditions, reducing travel times and improving overall efficiency. By leveraging up-to-the-minute information, you can avoid congested areas and potential delays, ensuring timely material deliveries and equipment arrivals at job sites.
Real-time traffic data integration enables sophisticated traffic incident analysis, allowing you to quickly identify and circumvent accidents, road closures, or other unexpected obstacles. This proactive approach minimizes the risk of delayed projects and enhances driver safety. Additionally, congestion impact assessment becomes more accurate, helping you make informed decisions about resource allocation and scheduling.
You'll benefit from reduced fuel consumption and vehicle wear as drivers spend less time idling in traffic. This not only cuts operational costs but also decreases your fleet's carbon footprint. By optimizing routes based on real-time data, you can improve on-time performance, meet project deadlines more consistently, and enhance client satisfaction. Ultimately, integrating real-time traffic data into your fleet management strategy leads to safer, more efficient operations and a competitive edge in the construction industry.
Multi-Stop Optimization Algorithms
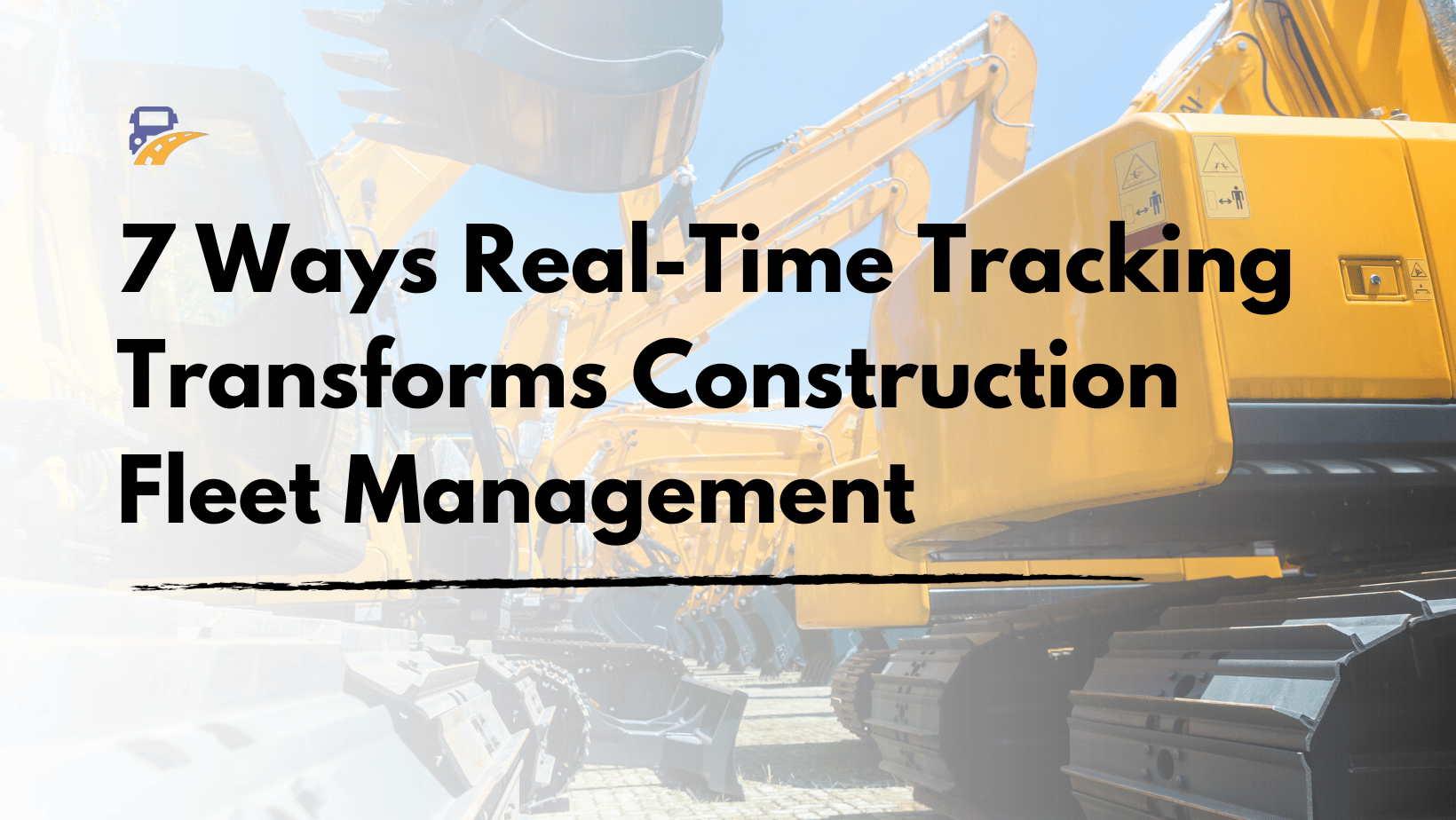
Multi-stop optimization algorithms represent a vital advancement in construction fleet management. These sophisticated systems utilize advanced computational techniques to enhance multi-stop routing efficiency, markedly improving overall fleet performance. By analyzing vast datasets, including traffic patterns, load requirements, and vehicle capabilities, these algorithms generate optimized routes that minimize distance and maximize resource allocation.
Key benefits of implementing multi-stop optimization algorithms include:
- Time savings: Reduced travel time between job sites, increasing productivity
- Load optimization: Efficient distribution of materials across multiple stops
- Fleet coordination: Improved synchronization of vehicles for streamlined operations
The algorithms' ability to incorporate real-time traffic prediction and adapt to changing conditions guarantees route flexibility. fleet tracking systems for construction, allowing for adaptive adjustments to delivery scheduling. This adaptability is essential in the construction industry, where project timelines and resource needs can shift rapidly
Geofencing for Efficiency
Leveraging geofencing technology, construction fleet managers can markedly enhance route planning and operational efficiency. By establishing virtual perimeters around job sites, equipment yards, and material suppliers, you'll gain real-time observations into vehicle movements and optimize resource allocation. Geofencing applications enable you to set up automated alerts for unauthorized entries or exits, strengthening security and guaranteeing compliance with regulations.
Geofencing Benefits | Geofencing Challenges | Geofencing Analytics |
---|---|---|
Improved safety | Initial setup costs | Real-time tracking |
Reduced fuel costs | Employee privacy | Performance metrics |
Enhanced productivity | Cellular coverage | Predictive maintenance |
While geofencing integration can present challenges, such as initial setup costs and potential cellular coverage issues, the long-term benefits far outweigh these obstacles (fleet tracking systems for construction). You'll experience improved safety measures, reduced fuel costs, and enhanced productivity across your fleet. Geofencing analytics provide significant data for performance metrics and predictive maintenance, allowing you to make informed decisions and optimize operations
To maximize geofencing benefits, focus on customization and scalability. Tailor virtual boundaries to specific project requirements and adjust them as needed. As your fleet grows, verify your geofencing technology can scale accordingly, maintaining efficiency and security across all operations.
Predictive Maintenance Scheduling
Predictive maintenance scheduling utilizes data analytics and machine learning to forecast equipment failures before they occur - fleet tracking systems for construction. You'll greatly reduce unexpected breakdowns by analyzing historical maintenance records, sensor data, and operational patterns to identify early warning signs of potential issues. By optimizing maintenance intervals based on actual equipment condition and usage, rather than fixed schedules, you'll maximize uptime and extend the lifespan of your construction fleet assets
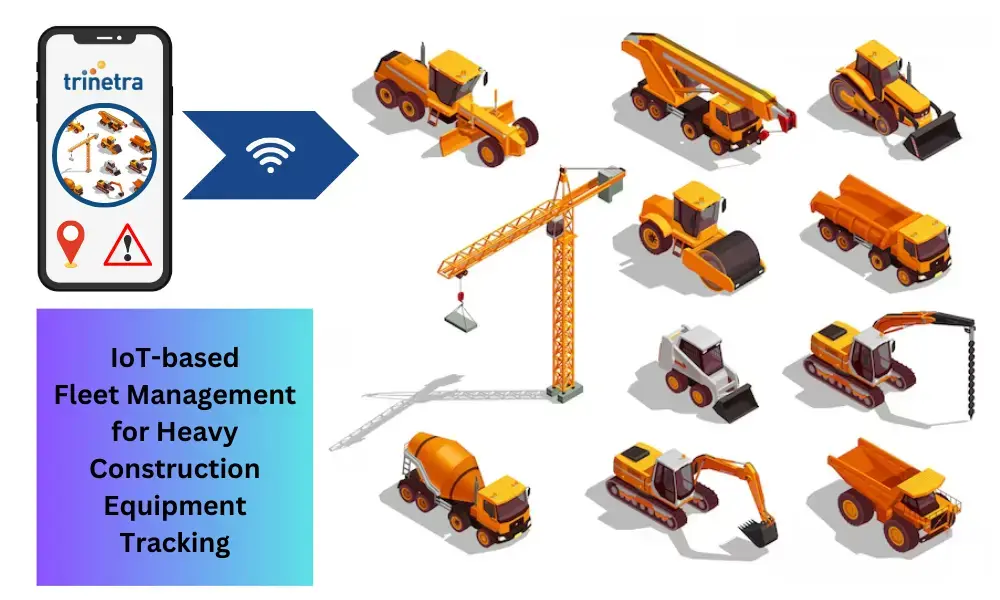
Prevent Unexpected Breakdowns
Unexpected breakdowns can cripple a construction fleet's productivity and profitability. To prevent these costly disruptions, implement a strong preventative maintenance program based on data-driven observations. Employ advanced tracking systems to monitor equipment performance, analyze patterns, and predict potential failures before they occur. This proactive approach greatly improves equipment reliability and minimizes the risk of unplanned downtime.
Incorporate breakdown analysis into your maintenance strategy to identify recurring issues and root causes. This data will inform targeted improvements and help prioritize maintenance tasks. Develop a thorough emergency response plan to address any unforeseen breakdowns swiftly and efficiently. Ascertain your team is well-trained and equipped to handle various scenarios, minimizing the impact on project timelines and overall fleet performance.
To (construction fleet tracking solutions)optimize your preventative maintenance efforts: (track construction vehicles with advanced systems)
- Establish a data-driven maintenance schedule based on equipment usage, age, and historical performance.
- Implement real-time monitoring systems to detect early warning signs of potential failures.
- Conduct regular inspections and maintenance checks, focusing on critical components and high-wear areas.
Optimize Maintenance Intervals
A well-tuned maintenance schedule is essential for maximizing fleet performance and minimizing downtime - fleet tracking systems for construction. To enhance maintenance intervals, you'll need to implement a data-driven approach that utilizes advanced tracking technologies. Start by analyzing historical maintenance logs and equipment performance data to identify patterns and predict ideal service timing
Implement a strong maintenance software system that integrates with your fleet tracking solution. This will enable you to schedule inspections based on actual usage hours, mileage, or specific operational conditions rather than arbitrary time intervals. Confirm your technicians receive regular training on the latest maintenance techniques and equipment-specific protocols to improve efficiency and accuracy.
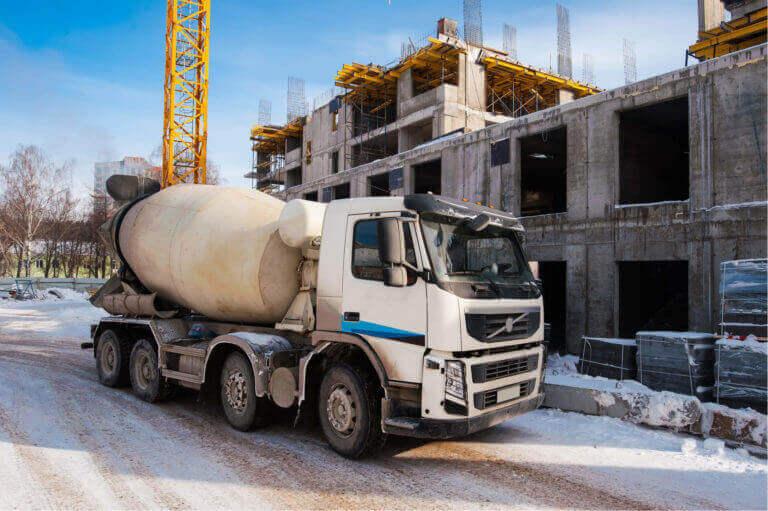
Maintain a thorough parts inventory system to reduce wait times for repairs and minimize equipment downtime. Regularly review and update your service contracts to align with your fleet's changing needs. Conduct routine compliance checks to verify all maintenance activities meet industry regulations - track construction vehicles with advanced systems and safety standards
Fuel Consumption Analysis
Through thorough fuel consumption analysis, construction fleet managers can gain significant understandings into their vehicles' efficiency and identify areas for improvement. By implementing fuel efficiency strategies and utilizing advanced consumption tracking tools, you'll be able to pinpoint inefficiencies and take corrective action. fleet tracking systems for construction. These data-driven observations can lead to substantial cost savings and reduced environmental impact
To conduct an effective fuel consumption analysis:
- Collect accurate data: Install telematics devices to monitor real-time fuel usage, idling time, and driver behavior.
- Analyze patterns: Use specialized software to identify trends in fuel consumption across different vehicles, routes, and operators.
- Implement targeted improvements: Based on the analysis, develop and execute specific strategies to address identified inefficiencies.
Driver Behavior Assessment
Evaluating driver behavior is a crucial component of optimizing construction fleet performance. By implementing advanced tracking systems, you'll gain important perspectives into your operators' habits and tendencies. These systems collect data on acceleration, braking, cornering, and speeding patterns, allowing you to conduct thorough risk assessments and identify areas for improvement.
To effectively utilize this information, establish clear performance metrics and implement behavior modification strategies. Create feedback loops that provide drivers with real-time information about their performance, encouraging self-correction and promoting driver safety - fleet tracking systems for construction. Complement this with regular training sessions focused on addressing specific issues identified through data analysis
Implement accountability measures to guarantee drivers take responsibility for their actions. Consider introducing incentive programs that reward safe driving practices and adherence to company policies. These programs can greatly enhance motivation and drive positive change across your fleet.
Asset Utilization Tracking
Asset utilization tracking forms the backbone of efficient construction fleet management. By implementing advanced tracking systems, you'll gain essential understandings into your equipment's performance and productivity. These data-driven observations enable you to make informed decisions about asset allocation, maintenance schedules, and replacement strategies.
Effective asset inventory management is vital for maximizing utilization rates and minimizing downtime. With real-time tracking, you can:
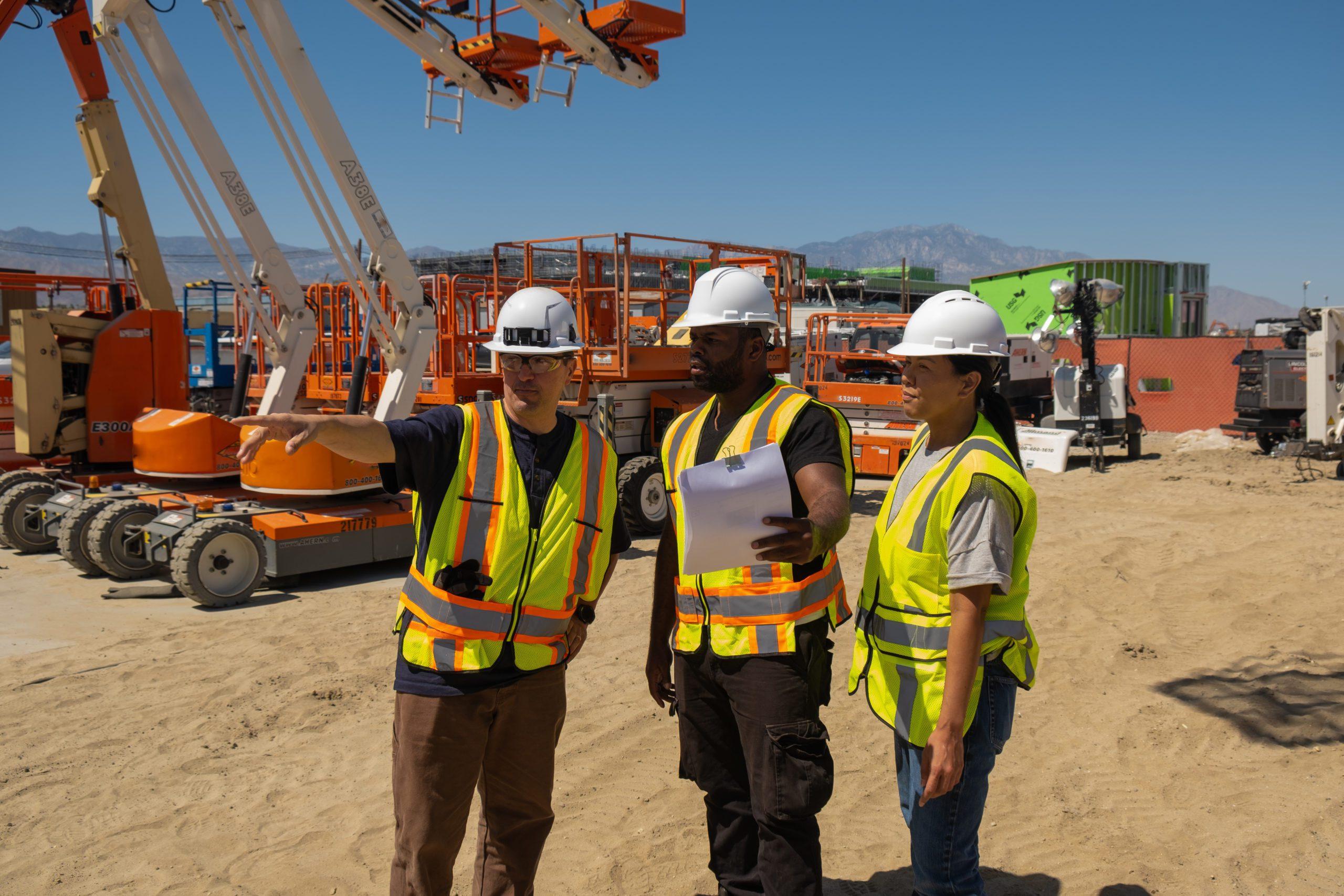
- Monitor equipment location and status
- Optimize resource allocation based on project needs
- Identify underutilized assets for reallocation or disposal
Equipment lifecycle analysis becomes more accurate and thorough with advanced tracking. You'll have access to detailed operational data. fleet tracking systems for construction, including hours of use, fuel consumption, and maintenance history. This information allows you to predict equipment lifespan more accurately, plan for replacements, and make data-backed decisions on whether to repair or replace aging assets
Automated Reporting Systems
Leveraging automated reporting systems can greatly enhance your construction fleet's operational efficiency. These systems considerably improve data accuracy by eliminating manual input errors and increasing reporting frequency. With user-friendly interfaces, you'll access real-time information on vehicle performance, maintenance schedules, and compliance tracking.
Integration capabilities allow you to seamlessly connect automated reporting with existing fleet management software, creating an extensive data ecosystem. This integration leads to significant cost savings through optimized resource allocation and reduced downtime. Automated systems excel at compliance tracking, guaranteeing your fleet meets all regulatory requirements and minimizing the risk of penalties.
Improved stakeholder communication is another key benefit, as automated reports can be easily shared with relevant parties. Historical analysis becomes more substantial, allowing you to identify trends and make data-driven decisions. These systems provide actionable perspectives, helping you proactively address potential issues before they escalate.
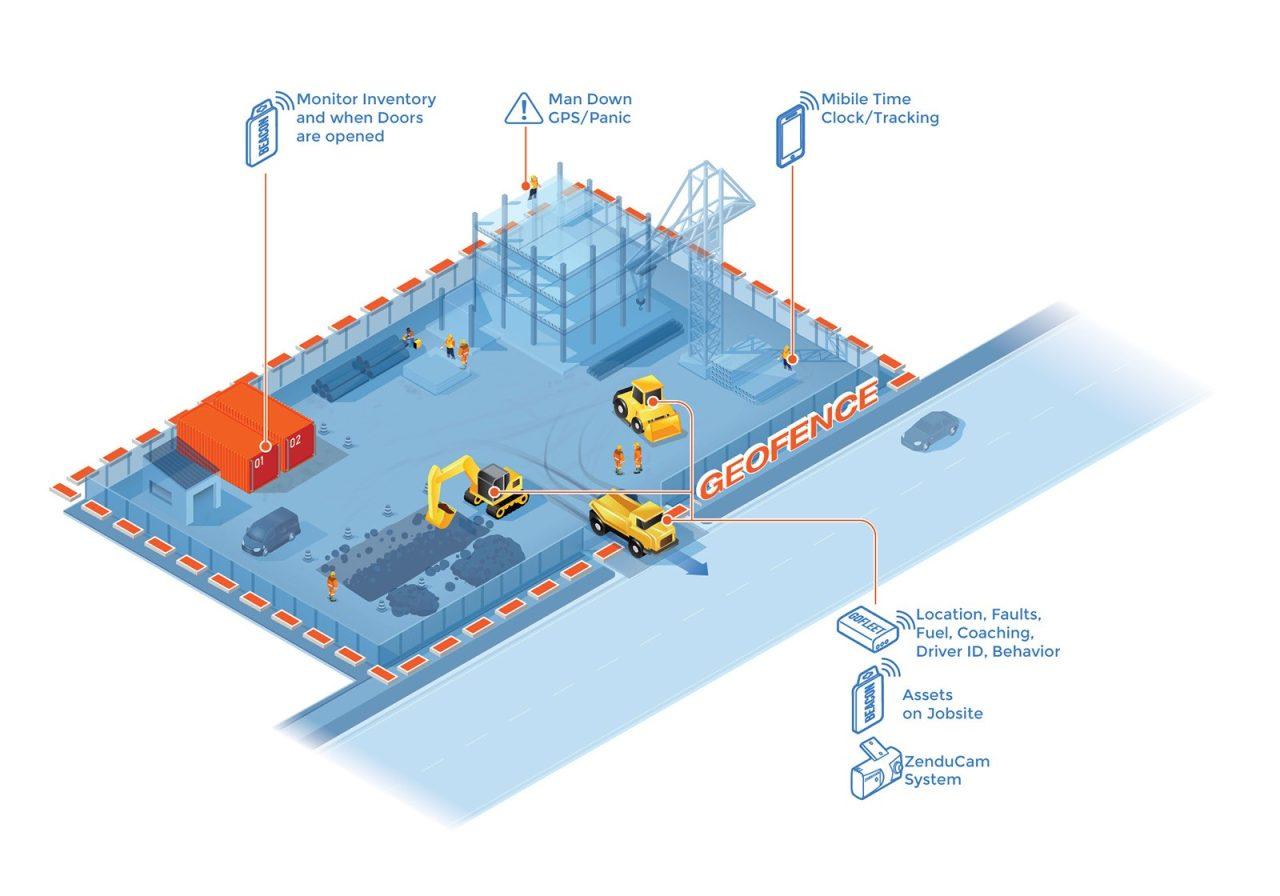
System scalability guarantees that as your fleet grows, the reporting infrastructure can adapt accordingly - fleet tracking systems for construction. By implementing automated reporting systems, you'll enhance safety, reduce operational costs, and gain a competitive edge in the construction industry
Geofencing for Site Management
Geofencing technology enables you to establish virtual boundaries around your construction sites, triggering automated arrival and departure notifications for equipment and vehicles. You'll gain real-time visibility into asset movements, allowing for precise tracking of equipment utilization and on-site time. This data-driven approach helps you optimize equipment distribution across multiple projects, ensuring the right resources are available when and where they're needed most.
Automated Arrival/Departure Notifications
Real-time location tracking revolutionizes site management through automated arrival and departure notifications. By leveraging geofencing technology, you'll receive instant arrival alerts when vehicles enter designated work zones and departure notifications when they exit. This automated system enhances safety and efficiency by:
- Eliminating manual check-ins, reducing human error and administrative overhead
- Providing accurate time-on-site data for improved project management and billing
- Enabling rapid response to unauthorized vehicle movements or potential security breaches
Automated notifications allow you to track vehicle dwell times, optimize resource allocation, and guarantee compliance with site-specific safety protocols (fleet tracking systems for construction). By analyzing arrival and departure patterns, you can identify bottlenecks, streamline traffic flow, and minimize idle time. This data-driven approach leads to increased productivity and reduced fuel consumption
Implementing automated arrival/departure notifications also enhances accountability. You'll have a verifiable record of vehicle movements, essential for resolving disputes and meeting regulatory requirements. By integrating this system with your existing fleet management software, you'll create a thorough summary of your construction fleet's performance, enabling data-backed decisions for continuous improvement and increased operational efficiency.
Optimize Equipment Distribution
An intelligent approach to equipment distribution can greatly enhance your construction site's efficiency. Geofencing technology allows you to implement advanced equipment allocation strategies and resource management techniques. By establishing virtual boundaries around your work sites, you can monitor and control the movement of machinery and assets in real-time.
Optimize your equipment distribution by leveraging geofencing data to analyze usage patterns and identify underutilized assets. This information enables you to make data-driven decisions about relocating equipment to areas of higher demand, reducing downtime and maximizing productivity. You'll also improve safety. fleet tracking systems for construction by ensuring that only authorized personnel operate machinery within designated zones
Implement resource management techniques such as flexible allocation based on project phases and workload fluctuations. Geofencing helps you track equipment location and utilization rates, allowing for precise scheduling and coordination of resources across multiple sites. By minimizing unnecessary equipment movement and optimizing distribution, you'll reduce fuel consumption, wear and tear, and potential safety risks associated with equipment transportation.
Use geofencing to create exclusion zones for hazardous areas or sensitive equipment, further enhancing site safety and preventing unauthorized access. This proactive approach to equipment distribution will streamline your operations, improve resource utilization, and contribute to a safer work environment.
Equipment Downtime Reduction
Despite the best efforts of construction managers, equipment downtime remains a notable challenge in optimizing fleet performance. To effectively reduce downtime, you'll need to implement a thorough strategy that addresses the root causes and utilizes data-driven solutions. By analyzing downtime causes and employing advanced tracking technologies, you can greatly improve equipment reliability and operational efficiency.
To achieve considerable reductions in equipment downtime: - fleet tracking systems for construction
- Implement predictive maintenance programs based on real-time performance metrics and historical data analysis
- Enhance maintenance training to guarantee technicians can quickly diagnose and resolve issues
- Employ workforce scheduling software to optimize resource allocation and minimize idle time
By adopting these strategies, you'll not only enhance productivity but also improve safety on your construction sites. Advanced tracking systems enable you to monitor equipment health in real-time, allowing for proactive interventions before critical failures occur. This approach reduces unexpected breakdowns and associated safety risks.
Furthermore, by integrating downtime analysis into your overall performance evaluation, you can identify patterns and trends that inform strategic decisions about equipment lifecycle management and technology adoption. This data-driven approach promotes continuous improvement in your fleet's operational efficiency and reliability.
Integration With Project Management
Seamlessly integrating construction fleet management with project management systems can dramatically enhance overall operational efficiency. By leveraging collaboration tools, you'll create a unified platform that streamlines resource allocation and task prioritization. This integration enables real-time data sharing between fleet operations and project timelines, allowing for more accurate timeline management and budget tracking.
Implement communication systems that facilitate instant information exchange between field teams and project managers. fleet tracking systems for construction. This guarantees that equipment deployment aligns with project milestones and reduces idle time. Integrated risk assessment modules help you identify potential delays or safety hazards related to fleet operations, allowing for proactive mitigation strategies
Utilize data analytics to optimize stakeholder engagement by providing thorough reports on fleet performance and its impact on project progress. This transparency cultivates trust and enables informed decision-making - construction vehicle tracking system. By synchronizing fleet management with project management software, you'll gain a complete view of your operations, allowing for more efficient resource utilization and improved project outcomes
Frequently Asked Questions
How Much Does Advanced Tracking Technology Typically Cost for a Construction Fleet?
You'll find advanced tracking costs vary widely based on fleet size and features. Conduct a cost comparison considering your budget constraints. Typically, expect $20-$150 per vehicle monthly, with potential ROI offsetting initial investment for enhanced safety and efficiency.
What Are the Privacy Concerns Associated With Tracking Construction Fleet Vehicles?
Like a watchful guardian, advanced tracking raises privacy concerns. improving construction fleet performance. You'll face data security challenges and employee monitoring issues. It's essential to implement strong encryption, establish clear policies, and communicate transparently to address workers' safety and privacy apprehensions
How Long Does It Take to Fully Implement an Advanced Tracking System?
You'll typically see full implementation of an advanced tracking system in 2-4 months. The timeline varies based on fleet size and complexity. You'll experience tracking system benefits, including improved safety, within weeks of initial deployment.
Can Advanced Tracking Systems Integrate With Existing Construction Management Software?
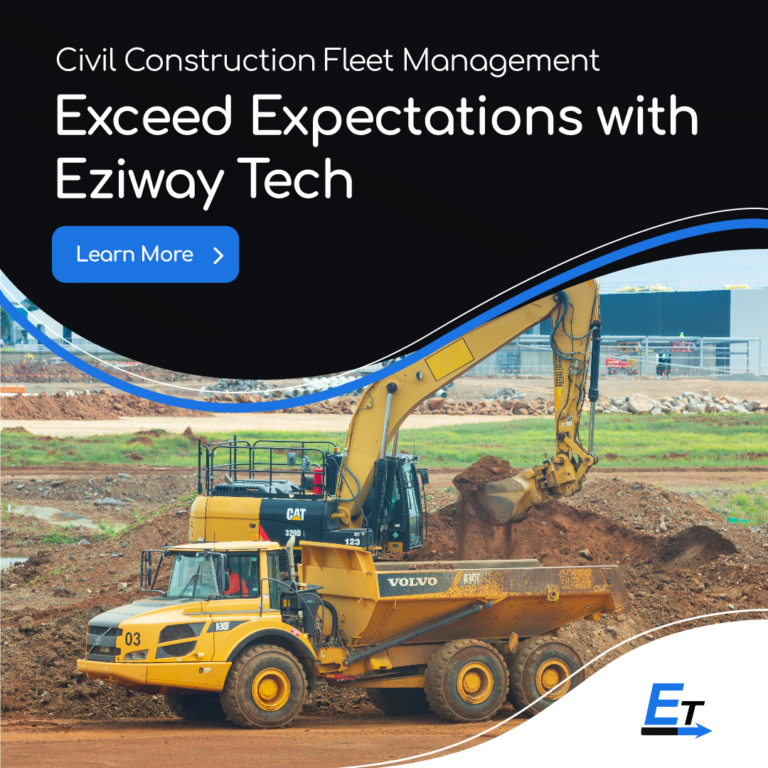
Oh, you thought your software was special? Brace yourself! Advanced tracking systems can indeed integrate with your existing construction management software. Data synchronization and software compatibility guarantee seamless operations. You'll experience enhanced safety and efficiency through this technical integration.
What Training Is Required for Staff to Effectively Use Advanced Tracking Technology?
You'll need thorough staff training for effective technology adoption. Focus on data interpretation, system direction, and safety protocols. Implement hands-on sessions, online modules, and ongoing support to guarantee proficiency with advanced tracking tools and reporting features.
Conclusion
You've now seen how advanced tracking can revolutionize your construction fleet's performance. By implementing these strategies, you'll optimize operations, reduce costs, and increase productivity. Consider this: companies using telematics report an average 12% reduction in fuel costs. That's significant savings for your bottom line. As technology continues to evolve, staying ahead with data-driven fleet management isn't just an option—it's a necessity for maintaining a competitive edge in the construction industry.