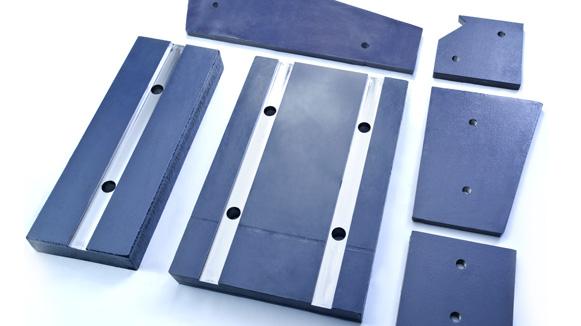
Selecting the correct crusher is important for every process. Understanding the stages of crushing and the types of crushers that are best suited to each stage simplifies equipment selection. Every crusher type is unique and designed to get a particular final result.
Similar to the previous stage every crushing stage will be expected to generate an exact output in the subsequent phase. Aggregate producers that match the correct shredder parts stage with the proper stage will be the most efficient and profitable.
Crushing stages
Aggregate producers are accustomed to selecting crushing equipment. They know that it is possible to choose the correct equipment piece based upon specifications and calculative gradation. Still, theoretical conclusions should always be evaluated against practical experience regarding the materials at hand as well as of the operational, maintenance and economical aspects of different solutions.
Typically, material reduction is handled in stages. Although there are single crusher options, the most popular systems contain at least two or more crushing stage.
Primary crushing. The primary crusher is first and foremost all making it possible to move material along a conveyor belt. In most aggregate crushing facilities, the primary crushing process is performed using a jaw crusher but a gyratory primary crushing machine could be utilized. An impact crusher could be an ideal choice if the material is easy to crush and not too hard.
The most important characteristics of a primary crusher are the capacity and ability to accept raw material without blockages. The larger primary crushers are more costly to purchase than smaller machines. This is why costs of investment for primary crushers are weighed against the cost of reducing raw materials to a smaller size.
Most often, trucks transport the raw materials to a fixed primary. The expenses of maintenance, fuel, tires and return on investment need to also be considered.
In cases where the quarry's face is crushed, pit-portable primary crushing plants could be a cost-effective option. Modern plants often require the possibility of a mobile primary crusher that is able to move in tandem with the quarry's surface.
Intermediate (secondary crushing). The purpose of intermediate crushing is to create various coarser fractions or to prepare materials to be crushed in the final stage. The quality of the final product is essential when the intermediate crusher will be used as ballast for railways.
In other cases, there are no conditions for quality, but the product must be suitable to fine crush. In the majority of cases, the goal is to achieve the highest reduction possible at the lowest possible cost.
Fine crushing (tertiary). This stage determines the quantity and quality of fine products. Final products may have strict specifications for quality, especially for the industry of aggregates.
In most instances fine crushing and cubicization processes are combined into a single crushing stage. Experience in the field as well as the theoretical understanding are essential when choosing a crusher to use to crush secondary materials. This is why manufacturers should ensure that they contact an experienced specialist in applications to make sure a system is properly engineered.
Types of crushers
Jaw crushers
A jaw crusher is one of the types of compression crushers. It can reduce the size of material by pressing it between two pieces steel. The discharge size is controlled by setting the space between those two steel pieces. The setting is more precise, which results in less output and a lower capacity for throughput.
As a compression crusher jaw crushers typically produce the most coarse material since they break rock through the natural lines of weak points. Jaw crushers are a fantastic primary crusher when used to prepare rock for subsequent processing steps.
Cone crushers and gyratory crushers
These machines also crush steel between two pieces of steel. The difference in the setting between the two pieces determines the output.
Although the chamber is round in shape, the moving piece of steel isn't meant to rotate. Instead, the wedge is used to press down one side of the chamber, while discharge ports are made on the other side. Cone crushers are employed for secondary and tertiary roles as an alternative to impact crushers when the shape of the crusher is a major requirement however, the amount of fines produced needs to be kept to a minimum.
Impact crushers
Impact crushers use mass and velocity to reduce the amount of feed material. First, the material feed is reduced when it enters the shredder parts by moving blow bars or hammers within the rotor. The secondary breakage occurs when the material is then accelerated to stationary aprons as well as breakers plates.
Impact crushers tend to be utilized when shape is an important requirement and the material used for feed is not extremely rough. The crushing action of an impact crusher breaks rocks along natural cleavage lines, which results in better quality products in terms of shape.
Final thoughts
When choosing the crusher that will best meet your requirements it is crucial to comprehend your needs for each stage.
In the first stage, look to get material to a size your conveyors and other processing machines can handle.
Certain operations require further crushing during the secondary and third crushing phases. These stages provide better control over the size and shape of the final product.
You can increase the effectiveness of your crusher and maximize your profits by matching the appropriate jaw crusher to the appropriate stage.