Z informacji tych wynika, że starożytność wielu budynków jest po prostu zmyślona, a my nie wiemy zbyt wiele, ktoś uważa, że nie musimy tego wiedzieć;
Jest to formuła naszych pradziadków, która została zachowana do dziś.
„Weź piasek z mierzei rzecznej.
Spal sto drzew i zbierz popiół.
Weź glinę i mieszaj, aż uzyska konsystencję mleka.
Dodaj wapno gaszone do płynnej gliny.
W drugim wiadrze wymieszaj piasek i popiół w stosunku 100 do 1.
Wszystko wymieszaj i dobrze wymieszaj.
Wlać do formy.”
Wlać do formy.”
Potem możesz rzeźbić starożytność, ile chcesz.
Oto nowoczesne technologie, podaję link: BETON GEOPOLIMEROWY
Oto nowoczesne technologie, podaję link: BETON GEOPOLIMEROWY
Technologia nakładania granitu na marmur jest wciąż tajemnicą.
„ Pokonałem marmur i uczyniłem go elastycznym jak wosk ” – Bernini , XVII-wieczny rzeźbiarz włoski . Wielcy mistrzowie mieli sporo tajemnic ukrytych – mieli je dmuchacze szkła, kowale, lutnicy, kucharze itp. I nie byłoby w tym nic dziwnego, gdyby tajemnica poszła do grobu wraz z ostatnim mistrzem, który nie potrafił (lub nie chciał) przekazać technologii swoim potomkom. Może się to zdarzyć w przypadku odlewania kamienia i starożytnego betonu.
Te dzieła sztuki w niczym nie ustępują egipskim
To nie jest granit, to także wysokiej jakości tynk wykonany z tworzywa polimerowego.
Kolejna ciekawostka: w czasach przed Piotrowych głównym składnikiem eksportu był potas, który według dzisiejszych standardów był bezużyteczny. Prawdopodobnie aż 90% całego eksportu z Pskowa do Europy stanowił węglan potasu (K2CO3). A jest to produkt otrzymywany właśnie z popiołu drzewnego. Ale na początku XVIII wieku Piotr I wydał dekret całkowicie zakazujący wywozu potażu z Rosji bez jego osobistej wiedzy, pod groźbą ciężkiej pracy przez całe życie. W tamtym czasie węglan potasu był surowcem strategicznym. Jeśli w Egipcie do produkcji sztucznego granitu używano węglanu potasu, to w Rosji istniały niezliczone złoża węglanu sodu, który służył jako spoiwo do betonu geopolimerowego. I to właśnie data dekretu stała się odpowiedzią na pytanie, kiedy właściwie pojawił się „antyk”. Okazuje się, że cała starożytność Europy i Bliskiego Wschodu powstała nie tak dawno temu (i nie przed naszą erą), a jej wytworzenie wymagało niesamowitych ilości głównej substancji, która pełni rolę spoiwa, w roztworze, który następnie uchodził za naturalny marmur, granit, malachit, dioryt itp. Ponadto należy zaznaczyć, że potas był głównym surowcem do produkcji szkła i... prochu! Teraz wypompowują gaz, ale wcześniej eksportowali potas. A Peter postanowił zakręcić kran w Europie, gdzie produkowano płytki porcelanowe keramomarazzi i proch strzelniczy.
W „Opowieści o carze Saltanie, jego synu, chwalebnym i potężnym bohaterze księciu Gwidonie Saltanowiczu i pięknej księżniczce łabędzi” Puszkina nie jest trudno znaleźć ślad handlu potasem. Przeczytajcie sami miejsce, w którym trzykrotnie kupcy meldują się carowi i księciu Guidonowi:
„Podróżowaliśmy po całym świecie,
handlowaliśmy sobolami,
lisami srebrnymi;
...
Handlowaliśmy końmi,
ogierami All Don,
...
Handlowaliśmy stalą damasceńską,
czystym srebrem i złotem,
...
Nie bez powodu handlowaliśmy
towarami nieokreślonymi ;
Ale droga jest dla nas daleka:
z powrotem na wschód...
To właśnie „nieokreślone towary”, którymi kupcy handlowali z tak dużym zyskiem, nie tylko nie były ujawniane, ale także podlegały najściślejszemu raportowaniu przed królem.
Z informacji tych wynika, że starożytność wielu budynków jest po prostu zmyślona, a my nie wiemy zbyt wiele, ktoś uważa, że nie musimy tego wiedzieć;
Jeszcze bardziej złożoną alegorią jest pomnik (ojcu księcia Raimondo - Antonio de Sangro (1685-1757). Włoska nazwa tego pomnika Disinganno jest często tłumaczona na język rosyjski jako „Rozczarowanie”, ale nie w obecnie powszechnie przyjętym znaczeniu , ale w języku cerkiewno-słowiańskim - „Wybawienie od zaczarowania” (Capella San Severo, w Neapolu)
„Wybawienie od zaczarowania” (po 1757 r.) wykonany przez Francesco Quirolo i jest najsłynniejszym z jego dzieł. Pomnik jest cenny ze względu na najwspanialsze dzieła w marmurze i pumeksu , z których wykonana jest sieć. Quirolo był jedynym z neapolitańskich mistrzów, który zgodził się na tak delikatne dzieło, reszta odmówiła, wierząc
, że jednym dotknięciem noża sieć rozpadnie się na kawałki. http://chispa1707.livejournal.com/983054.html
Z informacji tych wynika, że starożytność wielu budynków jest po prostu zmyślona, a my nie wiemy zbyt wiele, ktoś uważa, że nie musimy tego wiedzieć;
W „Opowieści o carze Saltanie, jego synu, chwalebnym i potężnym bohaterze księciu Gwidonie Saltanowiczu i pięknej księżniczce łabędzi” Puszkina nie jest trudno znaleźć ślad handlu potasem. Przeczytajcie sami miejsce, w którym trzykrotnie kupcy meldują się carowi i księciu Guidonowi:
„Podróżowaliśmy po całym świecie,
handlowaliśmy sobolami,
lisami srebrnymi;
...
Handlowaliśmy końmi,
ogierami All Don,
...
Handlowaliśmy stalą damasceńską,
czystym srebrem i złotem,
...
Nie bez powodu handlowaliśmy
towarami nieokreślonymi ;
Ale droga jest dla nas daleka:
z powrotem na wschód...
To właśnie „nieokreślone towary”, którymi kupcy handlowali z tak dużym zyskiem, nie tylko nie były ujawniane, ale także podlegały najściślejszemu raportowaniu przed królem.
Z informacji tych wynika, że starożytność wielu budynków jest po prostu zmyślona, a my nie wiemy zbyt wiele, ktoś uważa, że nie musimy tego wiedzieć;
Rzeźba nazywa się „Pijany Satyr” 200 p.n.e. Muzeum Włoch.
Wcześniej sądzono, że to marmur, ale nieświadomy student postanowił sfotografować siebie siedzącego na kolanach rzeźby wykonanej przez „nieznanego rzeźbiarza” i przypadkowo zranił się w nogę. nie dla siebie, ale dla satyry!„Gwałt Prozerpiny”
Rzeźba „Gwałt Prozerpiny”. Marmur. Wysokość 295 cm. Galeria Borghese, Rzym. Lorenzo Bernini stworzył to arcydzieło, gdy miał 23 lata. W 1621 r . „ Pokonałem marmur i uczyniłem go elastycznym jak wosk ”.Jeszcze bardziej złożoną alegorią jest pomnik (ojcu księcia Raimondo - Antonio de Sangro (1685-1757). Włoska nazwa tego pomnika Disinganno jest często tłumaczona na język rosyjski jako „Rozczarowanie”, ale nie w obecnie powszechnie przyjętym znaczeniu , ale w języku cerkiewno-słowiańskim - „Wybawienie od zaczarowania” (Capella San Severo, w Neapolu)
„Wybawienie od zaczarowania” (po 1757 r.) wykonany przez Francesco Quirolo i jest najsłynniejszym z jego dzieł. Pomnik jest cenny ze względu na najwspanialsze dzieła w marmurze i pumeksu , z których wykonana jest sieć. Quirolo był jedynym z neapolitańskich mistrzów, który zgodził się na tak delikatne dzieło, reszta odmówiła, wierząc
, że jednym dotknięciem noża sieć rozpadnie się na kawałki. http://chispa1707.livejournal.com/983054.html
Trochę o tym, co kryje marmurowa muszla...
Kolumna marmurowa (wzmocniona prętami zbrojeniowymi) z 1075 r. Cypr. Wyciągnij własne wnioski.
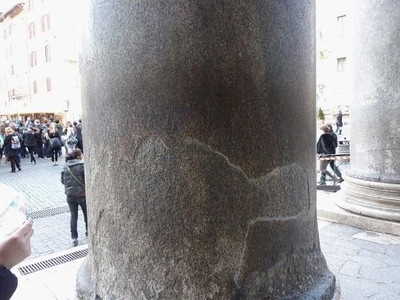
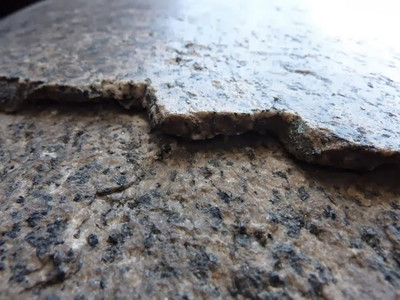
Fragmenty kolumn Panteonu.
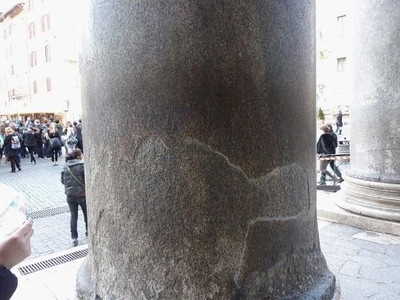
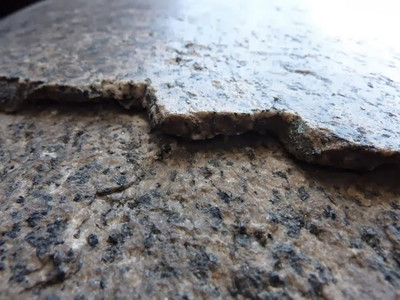
Fragmenty kolumn Panteonu.
Na tym łączu znajduje się duża liczba posągów, to będzie interesujące: Czy to jest kamień?
Z informacji tych wynika, że starożytność wielu budynków jest po prostu zmyślona, a my nie wiemy zbyt wiele, ktoś uważa, że nie musimy tego wiedzieć;
Jest to formuła naszych pradziadków, która została zachowana do dziś.
„Weź piasek z mierzei rzecznej.
Spal sto drzew i zbierz popiół.
Weź glinę i mieszaj, aż uzyska konsystencję mleka.
Dodaj wapno gaszone do płynnej gliny.
W drugim wiadrze wymieszaj piasek i popiół w stosunku 100 do 1.
Wszystko wymieszaj i dobrze wymieszaj.
Wlać do formy.”
Wlać do formy.”
Potem możesz rzeźbić starożytność, ile chcesz.
Oto nowoczesne technologie, podaję link: BETON GEOPOLIMEROWY
Oto nowoczesne technologie, podaję link: BETON GEOPOLIMEROWY
Kompozycje geopolimerowe w starożytności.
Domowe przepisy http://sibved.livejournal.com/73527.htm l
Oryginał zaczerpnięty z chispa1707 w Geopolimery przeszłości
Kopiuję fragment podręcznika rzemieślniczego z wydania z 1931 roku. Istnieje mnóstwo przepisów, począwszy od tego, jak nadać gipsowemu posągowi wygląd antycznego brązu, jest granit, jest marmur – my, nie-rzemieślnicy, nie moglibyśmy marzyć o takiej różnorodności.
Jeśli skorzystasz z linku, możesz pobrać całą książkę.
Jeśli skorzystasz z linku, możesz pobrać całą książkę.
1. Sztuczny marmur według Borchardta
1.1. Masę przygotowuje się z czystego piasku kwarcowego, wapna gazowanego, talku i gipsu, do których można dodać drobno zmielony barwnik. Stosowany piasek musi składać się z czystej krzemionki i w tym celu jest myty i oczyszczany ze wszystkich składników organicznych. Po całkowitym wyschnięciu piasku dodaje się do niego 5-6% tripoli. Następnie jako środek wiążący na każde 100 sztuk piasku dodaje się 6-7 wapna gazowanego, 3 talku, 4 gipsu, 3 skalenie. Wszystkie składniki miesza się razem z niewielką ilością wody. Powstałą masę układa się w foremkach i po całkowitym wyschnięciu wypala w białym ogniu w piekarniku bez dmuchawy.
1.2. Weź 80 gipsu i 20 węglanu wapna, drobno zmiel, wymieszaj i ugniataj z mieszaniną składającą się z 1000 wody destylowanej i 1080 siarczanu wapna.
1.3. Weź 1000 wody, 1440 kleju, 1000 kwasu siarkowego. Następnie wkładają ciasto do foremek, a gdy stwardnieje, wyjmują je, suszą przez dwie godziny, mielili i polerowali w zwykły sposób. Na koniec przedmiot zanurza się w kąpieli z oleju lnianego o temperaturze 70°, po czym suszy się go i smaruje stearyną. Do barwienia zalecane są barwniki anilinowe.
1.4. Sztuczny marmur jest bladożółty do białego. 30 gruby biały piasek, 42 kreda, 24 kalafonia, 4 wapno palone.
1.5. Zielonkawy. 28 gruby biały piasek, 42 kreda, 2 ultramaryna, 24 kalafonia, 4 wapno palone.
1.6. cielesne. 28 gruby biały piasek, 42 kreda, 1 ultramaryna, 1 cynober, 24 kalafonia, 4 wapno palone.
2. Imitacja marmuru
2.1 Według Van der Steena. Najpierw przygotuj wodę, w której gips będzie mielony, dodając do niej klej do drewna i żywicę; Klej rozpuszcza się w ciepłej wodzie w zwykły sposób, a żywicę rozpuszcza się w ciepłej kąpieli terpentynowej. Gips rozcieńcza się w tak przygotowanej wodzie, tak aby cała masa wystarczyła do wypełnienia formy. Następnie do mieszaniny dodaje się farby niezbędne do malowania marmuru; farby należy przygotowywać w specjalnych naczyniach. Tak przygotowany i zabarwiony marmur wlewa się następnie do form gipsowych, cementowych lub gumowych, tworząc równe płyty na płytach szklanych lub kamiennych. Tę warstwę marmuru nakłada się na grubość 4 mm, następnie przesiewa się na nią warstwę suchego tynku, aby usunąć nadmiar wody użytej do rozpuszczenia kolorowego tynku. Po dokładnym zwilżeniu tej warstwy sproszkowanego gipsu wodą zawartą w nadmiarze w kolorowym gipsie, wylewa się na nią cienką warstwę dobrze rozpuszczonego, ale nie zabarwionego gipsu i wylewa się na nią płótno lub płytę. Następnie nakładana jest warstwa rozpuszczonego gipsu, do której dodawany jest pokruszony kruszony kamień. Ta ostatnia warstwa zależy od grubości, jaką chcesz nadać przedmiotowi wykonanemu ze sztucznego marmuru. Po dostatecznym stwardnieniu masy (po 6-8 godzinach) wyjmuje się ją z płyty lub wyjmuje z formy, przeciera pumeksem i pory w masie wypełnia się rozpuszczonym gipsem, malując na kolor podstawowy odlany obiekt. Aby powierzchnia stała się wodoodporna , należy ją pokryć krzemianem potasu, zanurzając ją w kąpieli lub rozprowadzając płyn za pomocą pędzla. Po całkowitym wyschnięciu masy powierzchnię poddaje się polerowaniu, a nowością procesu polerowania jest to, że poleruje się ją za pomocą wacika owiniętego w szmatkę i nasączonego pastami wykonanymi według specjalnych receptur:
2.1.1. Biała pasta do jasnego sztucznego marmuru: 100 bielona guma, 600 alkohol, 25 drobno zmielony gips.
2.1.2. Brązowy lakier: 100 pomarańczowy gumowy lakier, 600 alkohol, 25 drobno zmielony gips. Najpierw przeciera się przedmiot przeznaczony do polerowania wacikiem nasączonym alkoholem, następnie kolejnym wacikiem nanosi się pastę i wacik wciera się dalej, aż do uzyskania widocznej przyczepności. Utworzoną w ten sposób warstwę lakieru szlifujemy pierwszym wacikiem nasączonym alkoholem, aż do uzyskania całkowicie gładkiej powierzchni.
2.1.3. Czarny połysk. Aby to zrobić, nałóż na szmatkę odrobinę czarnej farby anilinowej. Aby uzyskać równomierny i bardzo błyszczący lakier należy co jakiś czas zwilżyć szmatkę zakrywającą tampon kilkoma kroplami olejku.
2.2. Według rozmiaru. Przedmioty - wazony, figury itp. - wykonane ze zwykłego wapienia podgrzewa się przez 12 godzin pod ciśnieniem 5 atmosfer wrzącą wodą lub parą. Następnie umieszcza się je w kąpieli składającej się z roztworu ałunu o temperaturze 5°B, w której pozostają od 1 dnia do kilku tygodni. W ten sposób kamień zyskuje większą twardość i zdolność przyjmowania połysku. Jeśli chcą pokolorować kamień, do mieszaniny dodaje się barwniki anilinowe rozpuszczone w wodzie.
2.3 Według Ostermeyera. Mleko wapienne mieszamy z drobno pokruszonym marmurem lub mleko wapno z kredą, aż do uzyskania konsystencji zawiesiny. Na podstawie badań cementu pompejańskiego Ostermeyer zaleca dodanie do tej masy wystarczającej ilości grubo pokruszonego kamienia wapiennego. Cement ten szybko schnie i twardnieje.
3. Imitacja granitu
Czysty, drobny piasek, piryt lub inną masę zawierającą krzemień wymieszać ze świeżo spalonym i kruszonym wapnem w proporcji: 10 sztuk piasku lub pirytu i 1 wapno. Wapno, gaszone wilgocią piasku, zjada krzemień i tworzy cienką warstwę wokół każdego ziarna krzemienia. Po ochłodzeniu mieszaninę zmiękcza się wodą. Następnie weź 10 pokruszonego granitu i 1 limonkę i wymieszaj je na miejscu. Obie mieszanki umieszcza się w metalowej formie tak, aby mieszanina piasku i wapna tworzyła sam środek przedmiotu, a mieszanina granitu i wapna tworzyła zewnętrzną powłokę o grubości od 6 do 12 mm (w zależności od grubości przygotowywanego przedmiotu ). Na koniec masę prasuje się i utwardza poprzez suszenie na powietrzu. Barwnikiem jest ruda żelaza i tlenek żelaza, które miesza się na gorąco z granitem.
Jeżeli chcą nadać przedmiotom utworzonym z powyższej kompozycji szczególną twardość, wówczas umieszcza się je na godzinę w krzemianie potasu i poddaje ogrzewaniu w temperaturze 150°C.
1. Albolite
Aby wytworzyć tę masę, magnezyt kruszy się i wypala na kawałki wielkości pięści w piecach retortowych, takich jakie są używane w fabrykach gazu. Magnezyt żelazny mielony jest na młynach, przesiewany przez sito i mieszany z odpowiednią ilością tripoli. Z tego proszku cementowego, rozpuszczonego w wodzie, można wykonać ozdoby, takie jak z gipsu, ale nie może on konkurować z gipsem. Ma jednak nieocenioną właściwość wytwarzania w połączeniu ze średnio mocnym roztworem chlorku magnezu twardej i plastycznej masy. Masa albolitowo-cementowa wymieszana w odpowiednich proporcjach, w zależności od jej przeznaczenia, powinna mieć konsystencję mniej lub bardziej gęstej zaczynu, który pod wpływem temperatury, w której pracują, stopniowo gęstnieje i po 6 godzinach. twardnieje. Kiedy masa stwardnieje na tyle, że nadal widać na niej ślady paznokci, zachodzi w niej proces samonagrzewania, zróżnicowany w zależności od wielkości i grubości wytwarzanego przedmiotu; Grube płyty nagrzewają się np. powyżej 100°C. Przy odlewaniu dużych obiektów jest to wada trudna do wyeliminowania, a formy samoprzylepne można stosować tylko z dużą ostrożnością. Przed rozpoczęciem procesu nagrzewania należy wyjąć obiekt z form klejowych. Przy odlewaniu małych przedmiotów nagrzewanie jest znikome i dlatego nie stanowi przeszkody. Plastyczność masy jest niezwykle wysoka. W przypadku ozdób gipsowych masa albolitowa ma tę zaletę, że jeśli pokryje się ozdobę gipsową cienką warstwą albolitu, powtarzając tę czynność do momentu, aż nic innego się nie wchłonie, wówczas ozdoba stanie się twardsza na zewnątrz.
W ten sam sposób można nadać większą wytrzymałość innym materiałom. Nie ma lepszego materiału do naprawy piaskowca niż cement albolitowy. Wieloletnie doświadczenie pokazało praktyczność smarowania domów albolitem. Wewnątrz domów bardzo praktyczne jest smarowanie stopni schodów, podłóg itp. Zaleca się pokrycie schodów drewnianych znajdujących się na zewnątrz warstwą albolitu.
2. Beeryt
Beeryt, materiał rzeźbiarski wynaleziony przez rzeźbiarza Beera w Paryżu, odpowiedni zarówno do najmniejszych, jak i największych odlewów, oddaje kontury i linie z precyzją, jakiej nigdy nie można osiągnąć za pomocą gipsu. Powierzchnia odlewów, którą można również polerować, jest czysto biała i ma prawie taki sam połysk i refleksy świetlne jak naturalny marmur. Masa ta szczególnie dobrze nadaje się do odlewania posągów, nadając podobnie jak marmur wrażenie miękkości i witalności, dzięki grze świateł i cieni. W pęknięciach beeryt ma strukturę krystaliczną, która charakteryzuje się dość dużą twardością. Odlana masa twardnieje w ciągu 1 godziny i tylko w rzadkich przypadkach wymaga dalszej obróbki. Beeryt składa się ze 100 pyłu marmurowego, 10-25 proszku szklanego, 5-10 przesianego sproszkowanego wapna, rozpuszczonego w płynnym szkle.
3. Marmoryt
Według Losse’a wytwarza się go z równych części drobno zmielonego, przemytego i podgrzanego magnezytu oraz z roztworu siarczanu magnezu. Obie części dobrze się miesza i wlewa do natłuszczonych foremek. Po stwardnieniu masę można umyć ciepłą wodą z mydłem. Utwardzona masa ma wygląd białego marmuru i z biegiem czasu nabiera twardości, dzięki czemu można z niej odlewać popiersia, posągi itp. Można w tym przypadku zastosować te same formy, które wykorzystywane są do prac gipsowych.
1. Farbowanie marmuru
1.1. Jak wiadomo, wszystkie kolorowe odmiany marmuru są bardzo drogie. W związku z tym popularne stało się ostatnio sztuczne barwienie tańszego białego marmuru. Metoda malowania jest następująca: niepolerowany marmur układa się poziomo i pokrywa roztworem barwiącym (patrz poniżej) tak gorącym, że jeszcze się pieni. Barwnik wnika wówczas głęboko w marmur i bardzo mocno przylega. Roztwór barwnika przygotowuje się w alkoholu. Aby zabarwić go na niebiesko, lakmus rozpuszcza się w alkoholu, a jego ilość jest całkowicie określona przez pożądaną gęstość koloru. Aby uzyskać żółty kolor, użyj roztworu gummigutu. A jeśli nałożysz drugi kolor (z gumą) na pierwszy kolor (z lakmusem), otrzymasz doskonały zielony kolor.
Przygotowany w ten sam sposób roztwór korzeni alkany, koszenili itp. barwi marmur na czerwono. Na koniec roztwór równych części siarczanu cynku, amoniaku i grynszu w alkoholu nadaje marmurowi złoty kolor. W rezultacie powstała bardzo efektowna mozaika, złożona z kawałków marmuru o różnych kolorach, pomalowanych w ten sposób. Pod względem urody i odporności na blaknięcie w niczym nie ustępuje mozaikom wykonanym z drogich gatunków marmuru, chociaż jest znacznie tańsza.
1.2. Nie każda farba nadaje się do malowania marmuru. Aby farba dobrze się przyjęła i dobrze kleiła, należy ją przygotować w następujący sposób: przygotować roztwór boraksu i barwnika roślinnego, a następnie dodać do tego roztworu kilka kropli kwasu azotowego lub trochę soli azotanowej. Na przykład, aby zabarwić marmur na niebiesko, przygotuj roztwór boraksu z indygo i dodaj kilka kropli soli żelazowo-azotowej (w postaci płynnej). Aby pomalować go na czerwono, rozpuść dowolny czerwony barwnik roślinny za pomocą boraksu i dodaj kwas azotowy. Zastępując barwniki orzechami atramentowymi, otrzymujemy doskonałą i trwałą czarną farbę do marmuru.
VII. Imitacja kamieni budowlanych1. Sztuczny kamień
1.1. 2 wapno hydrauliczne zmieszane z roztworem ałunu w 15-krotności ilości wody, 10 piasku i 1 cement miesza się w masę, którą wciska się do form i usuwa po 24 godzinach. Kamienie są gotowe do użycia po 14 dniach, ale z biegiem czasu stają się twarde.
1.2. Mieszankę 1 cementu i 3 piasku rozpuszcza się w rozcieńczonym kwasie siarkowym (100 wody na 2 kwasy) i prasuje pod silnym ciśnieniem. Kamienie suszy się na powietrzu przez dwa dni, umieszcza w rozcieńczonym kwasie siarkowym (2 kwasy na 100 wody) na 12 godzin i ponownie suszy.
1.3. 2 cementy portlandzkie, 1 piasek i 1 żużel miesza się na sucho, a następnie zwilża wodnym roztworem siarczanu żelazawego. Gęsty roztwór wciska się do foremek, suszy przez tydzień lub dwa w ciepłym miejscu, następnie zanurza w wodzie na 24 godziny i ostatecznie suszy przez 4 tygodnie.
1.4. 10 wapna palonego dokładnie wymieszać w 3-4 wodach, następnie dodać 40-60 suchego piasku i 2,5-10 cementu hydraulicznego i ponownie dobrze zmielić. Następnie masę wciska się do foremek.
1,5. 1 wyługowany popiół, 1 żywica, 1/8 - 1/4 oleju lnianego podgrzewa się w kotle, przy ciągłym mieszaniu, i wlewa do foremek.
1.6. 15 litrów wody po kleju, 1/4 litra wody, w której rozpuszczono klej do drewna i 1/8 kg sproszkowanego boraksu miesza się z taką ilością gipsu, aby uzyskać ciastowatą masę nadającą się do sprasowania. Mieszając barwniki uzyskuje się kolorową masę.
1.7. 300 kg piasku lub tłucznia kamiennego, 75 kg żywicy i 20 litrów smoły drzewnej miesza się z odpowiednią ilością zmielonych kamieni i, w zależności od pożądanego koloru, dodaje się czerwień wenecką lub gips i mocno podgrzewa.
1.8. 4 żwir i 1 cement, z dodatkiem kruszonego kamienia itp., w razie potrzeby, rozcieńcza się wodą. Masę układa się w formie, na którą nakłada się warstwę o grubości około 1/2 cm złożoną z 2 drobnego piasku, 1 cementu i 1 suchej farby mineralnej w proszku. Jeśli chcą ozdobić kamień wzorem na powierzchni, to odpowiedni wzór umieszcza się na dnie formy i na nim umieszcza się wspomnianą kolorową warstwę. Gdy kamień jest już prawie suchy, jego powierzchnię pokrywa się rozcieńczonym płynnym szkłem. (Niektóre ulice w Nowym Jorku są wyłożone takimi płytami).
1.9. 30 piasku kwarcowego i 1 tlenek ołowiu miesza się z 10 płynnego szkła i w razie potrzeby z odpowiednim barwnikiem, wciska do foremek, a następnie przez 2 godziny. wystawiony na działanie czerwonego ciepła.
1.10 Wapno hydrauliczne umieszcza się w koszu o pojemności około 1/8 tony i zanurza w naczyniu z wodą i pozostawia w nim do momentu, aż przestaną pojawiać się pęcherzyki powietrza. Następnie kosz wyjmuje się z wody, pozwala wodzie spłynąć i przykrywa kosz odwróconym żelaznym kociołkiem. Krawędzie kotła stojącego na podłodze są dookoła posypane popiołem, aby zapobiec wymianie powietrza pod kotłem. Wapno pozostawia się na 12 godzin, po czym zamienia się w drobny proszek. Proszek ten służy do produkcji kamieni. 1 część tego wapna miesza się z wodą tak, aby powstała płynna owsianka, do której dodaje się 2 1/2 kruszonego kamienia i 1/2 popiołu z węgla, torfu lub ługowanego popiołu drzewnego. Dokładnie wymieszaj mieszaninę i dodaj tyle wody, aby całkowita ilość zużytej wody była 4-krotnością ilości wapna. Wlać mieszaninę do foremek, gdzie wkrótce stwardnieje.
2. Kamienie budowlane wulkaniczne według Schroedera
Tzw. wulkaniczne kamienie budowlane wytwarza się z żużli węglowych i popiołów z dodatkiem wapna hydraulicznego i innych substancji wiążących. Rozdrabniacz zużywa 16 wapna hydraulicznego i 1 cementu portlandzkiego na 100 popiołów lub żużli węglowych. Masę tę rozdrabnia się, dobrze miesza, a następnie wciska do foremek. Zaleta tej metody polega na korzystnym wykorzystaniu zbędnych odpadów, których stale rosnąca ilość jest często uciążliwa, na znacznej wytrzymałości tych kamieni przy względnej lekkości, na dużej odporności na wpływy atmosferyczne i na niskich kosztach produkcji. . W Niemczech z tych wulkanicznych kamieni budowlanych zbudowano wiele masywnych domów mieszkalnych i budynków ze sklepieniami.
3. Masa kamienna według Mayera
Najpierw zmieszaj 5 wapna gaszonego z 5 wcześniej mocno podgrzanymi wapnem. 1 tę mieszaninę miesza się z 1 kredą, 2 piaskiem, 2 mączkami kwarcowymi lub szklanymi, 6 sproszkowanym fluorytem i dodaje tyle płynnego szkła potasowego (ciężar właściwy 1,3), aby uzyskać pastowatą masę, którą można łatwo wlać do foremek i twardnieć w ciągu 10-10- 40 minut Po wyschnięciu na powietrzu odlane przedmioty nasącza się naprzemiennie rozcieńczonym płynnym szkłem i kwasem fluorokrzemowym. W podobny sposób można traktować mieszaninę równych części sproszkowanego szkła i fluorytu stężonym płynnym szkłem. Do masy barwionej Mayer zaleca mieszankę 2 fluorytów, 1 kwarcu lub szkła i 1 farby, rozdrobnionych stężonym roztworem ciekłego szkła.
4. Masa kamienna według Steyera
Weź drobny piasek kwarcowy i dodaj, w zależności od pożądanego stopnia twardości, od 2 do 10% drobno zmielonego tlenku ołowiu. Im twardsze powinny być kamienie, tym więcej tlenku ołowiu zostanie pobrane. Aby uzyskać kolorową masę kamienną, należy dodać odpowiedni, drobno zmielony tlenek metalu, w zależności od pożądanego koloru. Następnie całą mieszaninę przesiewa się, aż dobrze się połączy. Następnie mieszaninę zwilża się jedynie płynnym szkłem sodowym lub potasowym, ponownie dobrze miesza, szczelnie prasuje lub ubija w formie i suszy w umiarkowanej temperaturze. Po wyschnięciu mieszaninę wypala się, w zależności od stopnia twardości, jaką chce się nadać wykonywanemu przedmiotowi, w mniej lub bardziej intensywnym ogniu. Należy również zauważyć, że płynne szkło nie powinno być zanieczyszczone siarczanem sodu, w przeciwnym razie kamienie ulegną erozji podczas suszenia.
5. Masa kamienna według Gephera
Nadaje się do tego dość miękka mieszanka wapna cementowego z płynnym szkłem potasowym, do której dodaje się odrobinę piasku rzecznego. Proporcja wapna cementowego do piasku rzecznego wynosi 2:1. Używając tej masy cementowej do naprawy schodów kamiennych, nie ma potrzeby odbijania zdeptanych stopni. Uszkodzone obszary zwilża się płynnym szkłem i nakłada na nie świeżo przygotowaną masę, której nadaje się niezbędny kształt stopni. Masa wysycha po 6 godzinach. i staje się twardy jak wapień.
6. Masa kamienna wg Schulte
Piasek 4-6 miesza się z 1 wapnem hydraulicznym i do mieszaniny dodaje się 6% suchego płynnego szkła, ewentualnie drobno pokruszonego na proszek. Następnie dokładnie miesza się i zwilża taką ilością wody, aby z tej masy można było uformować kamienie o pożądanym kształcie. Wymagane około 10% wody. Kamienie wykonane z tej masy pozostawia się do stwardnienia, co zajmuje 1-4 dni, po czym umieszcza się je w kadzi z wodą. Pod ciśnieniem wody płynny proszek szklany rozprowadzony równomiernie w masie rozpuszcza się i łączy z wapnem, które również w niewielkiej ilości rozpuszcza się z wody w sól krzemionkowo-wapniową. Gdy po kilku dniach płynne szkło rozpuści się i przekształci odpowiednią ilość wapna w nierozpuszczalną sól wapniowo-krzemionkową, kamienie umieszcza się w wodzie zawierającej 5% roztwór węglanu sodu. Dzięki temu pozostałe wolne wapno zamienia się w wapno gazowane, natomiast hydrat tlenku sodu rozpuszcza się i zmywa poprzez dokładne mycie stwardniałych już kamieni w wodzie. Następnie kamienie suszy się na powietrzu. Przy stosowaniu tej metody zasadniczym warunkiem jest, aby płynne szkło znajdowało się w stanie nierozpuszczonym w postaci proszku, a dopiero po rozpuszczeniu się całego płynnego szkła i utworzeniu się krzemianu wapnia kamienie należy zalać roztworem węglanu sodu. sól z limonką.
7. Masa kamienna wg Hightona
Metoda ta, stosowana przez firmę Victoria Stone Company z Londynu, polega na zmieszaniu drobnych fragmentów granitu z cementem hydraulicznym, a następnie po uformowaniu i stwardnieniu masę zanurza się w roztworze płynnego szkła. Fragmenty granitu kruszy się i na każde 4 granity dodaje się 1 cement portlandzki, a ciasto miesza się z wodą. Masę tę wlewa się do foremek, odstawia na 4 dni, a następnie podlewa 25% roztworem krzemianu sodu przez dwa dni. Wytwarzane w ten sposób kamienie sztuczne znajdują zastosowanie głównie jako kamienie budowlane, płyty schodkowe i chodniki.
8. Masa kamienna wg Dumenila
1100 gipsu, 10 wapna hydraulicznego, 5 żelatyny i 500 wody. Gips i wapno hydrauliczne rozcieńcza się w naczyniu żelatyną i wodą, dobrze miesza i jednorodną masę wlewa do drewnianych form łupanych, wstępnie nasmarowanych szarym mydłem. Po 20-22 minutach. usuń kamień z formy i wysusz go na powietrzu, co zajmie 14 dni. W razie potrzeby suszenie można przyspieszyć sztucznym ogrzewaniem. Kamienie można pomalować na dowolny kolor dodając do masy barwnik.
Te sztuczne kamienie można stosować do wszelkiego rodzaju prac budowlanych - budynków mieszkalnych, mostów, wodociągów itp. Kamienie odlane z tej masy mają taką samą wytrzymałość jak kamienie naturalne, a co szczególnie ważne, ściany z takich kamieni nie nie cierpieć z powodu wilgoci. Rzeczą oczywistą jest, że masę można odlać w dowolnym kształcie i w ten sposób można uzyskać różnorodne detale architektoniczne.
9. Masa kamienna wg Lebruna
Metoda ta polega na przekształceniu wapienia hydraulicznego w drobny proszek i zmieszaniu go z mąką węglową (3-4 wapienia hydraulicznego na 1 sproszkowany węgiel drzewny). Mieszankę rozdrabnia się z wodą na ciasto, z którego powstają cegły, które wypala się w piecu wapienniczym. Po wypaleniu masa ponownie przekształca się w drobny proszek i ten proszek, który Lebrun nazywa hydro, stanowi główny materiał do jego produkcji. Kamienie, które produkuje, są dwojakiego rodzaju. Jeden gatunek składa się z mieszaniny hydro i piasku w stosunku 1:3 i służy do produkcji ozdób architektonicznych - słupów, wsporników, parapetów itp. Drugi gatunek, składający się wyłącznie z mocno zagęszczonego hydro, służy do układania nawierzchni płyty itp. Masa formowana w formach żelaznych z dodatkiem takiej ilości wody, jaką formierze zużywają do zwilżania piasku. Udowodniono, że przedmioty przygotowane z tej masy zachowują swój prawidłowy kształt, są odporne na tarcie i nacisk, a także są niewrażliwe na wpływy atmosferyczne.
Starożytni Hindusi znali także technologie odlewania betonu, marmuru i granitu; oto zdjęcia ich świątyni Shravanabelagola